The pharmaceutical industry uses pure steam in many processes – from sterilization to cleaning. The requirements are high: the steam must be absolutely pure, free of impurities and produced from high-quality materials. JUMAG offers the perfect solution, presented at PharmaP.
Why is pure steam so important?
High-quality pure steam is essential for pharmaceutical processes. The water quality determines the purity: it must be extremely pure, with minimal conductivity and no dirt particles. All components are made of stainless steel or PVE to prevent corrosion and contamination. Almost complete degassing prevents additional corrosion.
JUMAG’s process for maximum purity
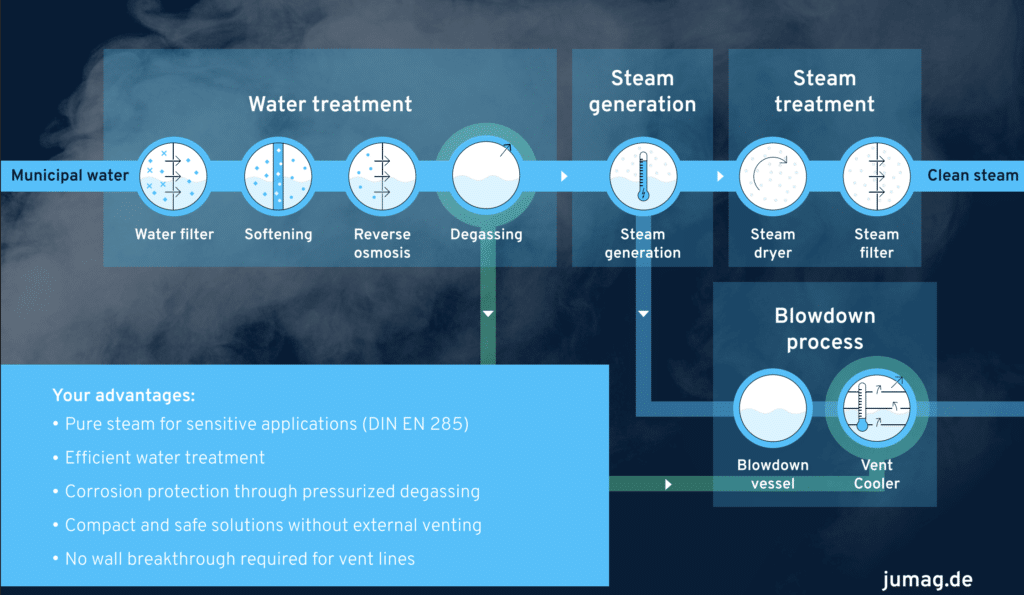
1. Water treatment
The pure steam process starts with the treatment of the city water. The water first passes through a raw water inlet module, which is equipped with a 30 µm backwash filter. This removes coarse impurities and provides initial cleaning. The water then enters a water softener, which removes magnesium and calcium. These substances contribute to water hardness and could cause deposits and limescale.
In the next stage, reverse osmosis drastically reduces the salt concentration to achieve a conductivity of just 5 microsiemens. If the city water has a particularly high conductivity, it undergoes additional deionization. This allows the water to be further optimized and the quality for pharmaceutical applications to be ensured.
2. Degassing & steam generation
The treated water, now referred to as permeate, is fed into the feed water tank (SWG). There, almost complete degassing takes place at a pressure of between 0.3 and a maximum of 0.5 bar. This process removes dissolved gases that could cause corrosion. Steam is then generated in an electric JUMAG steam generator. This converts the deaerated water into high-quality steam that meets the strict requirements of the pharmaceutical industry.
3. Steam processing for pure steam
After steam generation, the steam passes through several cleaning stages. A steam dryer removes any remaining residues and pollutants, as well as initial condensate. A fine-pored steam filter then ensures that even the smallest particles are removed from the steam. This produces steam of maximum purity that meets the high pharmaceutical standards.
4. Blow-down process and safe handling
The system must be cleaned regularly to ensure that steam is continuously generated at the highest level. Contaminated water is drained from the steam generator into a special blow-down collector (ASG). Another important step is the innovative VentCooler technology. This reduces the hot steam discharge to below 60 °C. This eliminates the need for external ventilation, which prevents structural measures such as wall openings for ventilation pipes.
The compact design and sophisticated safety concept make the JUMAG solution particularly user-friendly. Operators benefit from easy handling, high efficiency and maximum safety.
The advantages of JUMAG pure steam
JUMAG provides an energy-efficient and safe solution for the pharmaceutical industry. Optimum water treatment and innovative degassing produce perfectly purified pure steam that is ideal for sensitive applications. The efficient water treatment ensures optimized energy use, while the steam generator offers maximum corrosion protection through targeted degassing.
In addition, the compact and safe design enables operation without external ventilation and without complex structural interventions. This makes installation particularly simple and flexible.
Visit us at Pharma P and experience the advantages of JUMAG pure steam generation at first hand! We look forward to your visit.