Pressure degassing
Water contains oxygen and carbon dioxide. Both lead to corrosion in the steam system. The concentration of oxygen and carbon dioxide drops with increasing temperature. This effect is used to degas the feed water in the feed water container.
The JUMAG pressure degassing:
Function and Benefit
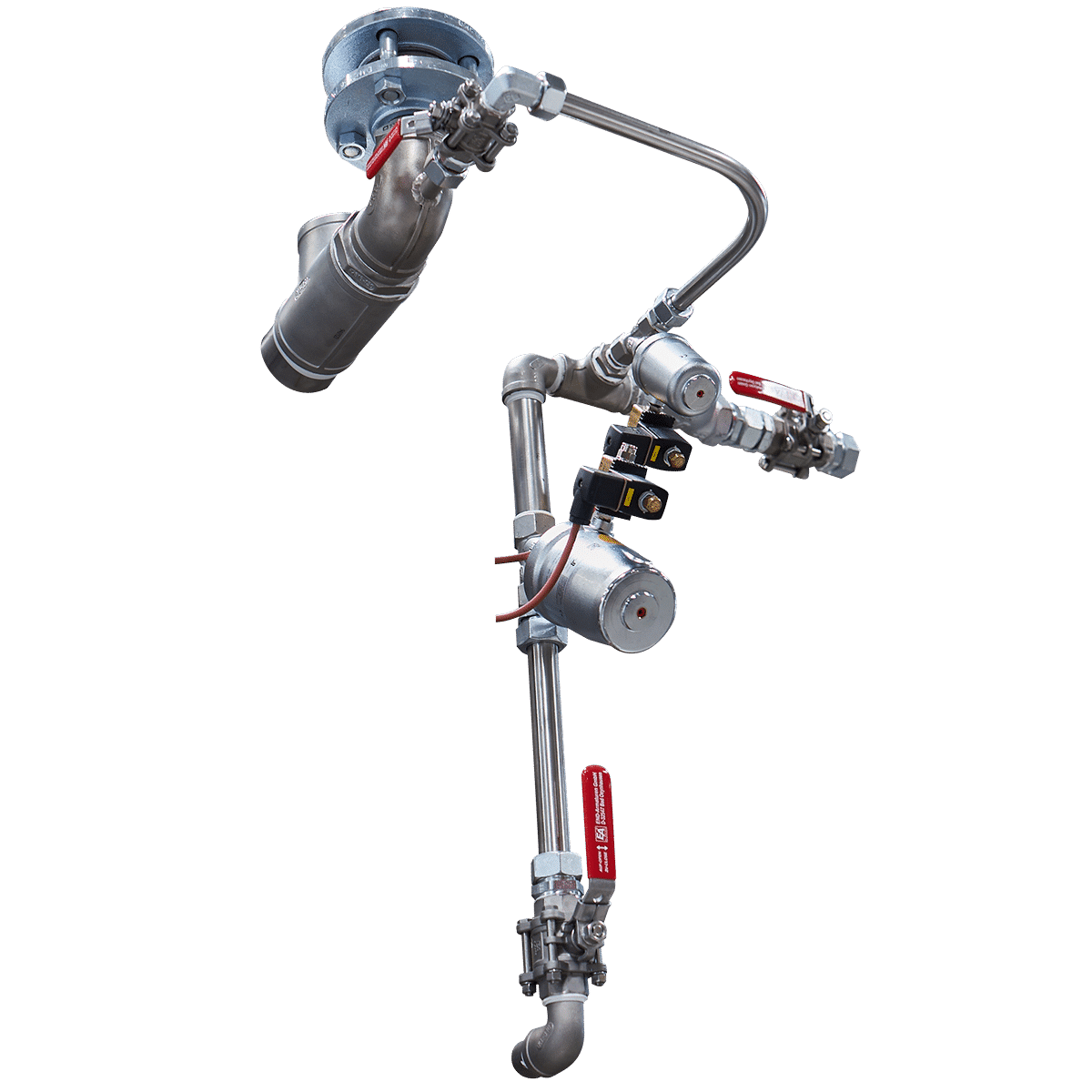
What is pressure degassing used for and what are its advantages?
Heating above 103°C minimises corrosive gases
In depressurised vessels where the temperature is usually at 90°C to 95°C, a large part of the oxygen and the carbon dioxide is driven from the water. However, not all gases escape, which can still quickly cause damage to steam lines and steam boilers unless they are bound with dosed solutions.
If the temperature of the feed water container is increased to more than 103°C, the concentration of oxygen and carbon dioxide is negligible.
Less dosed solutions required, less frequent blow down
Thus less dosed solutions are required. The reduced salt content of the dosage also has a positive influence on the blow down intervals.
To achieve a water temperature in excess of 103°C, the water must be pressurised. We then speak of pressure degassing or full degassing – in contrast to partial degassing at less than 100°C in depressurised vessels.
Additional energy savings
In addition, with a high proportion of condensate return flow, up to 1.6% (with a JUMAG steam boiler DG560 this corresponds to 6.5 kW) energy is saved
Further information about JUMAG pressure degassing
Available for all feed water containers
JUMAG offers pressure degassing for all JUMAG feed water containers in combination with the latest boiler control.
Patented Regulation: Higher savings compared to other systems
The patented JUMAG control of the venting valve saves significant energy compared to other systems, as venting only takes place when oxygen is present in the system.
The function in detail:
A temperature sensor measures the temperature in the feed water container and maintains it at the desired temperature (usually 100°C) by adding steam to the water area.
Likewise, the pressure in the feed water container is measured and maintained at the desired pressure.
A magnetic valve, which is activated depending on the fresh water supply (and thus the supply of O2 and CO2) is opened in cycles, the harmful gases are expelled from the feed water container together with a small amount of steam.
Safe and without TÜV monitoring or approval
The feed water container is supplemented by a relief valve that limits the pressure to 0.5 bar at most. The feed water container can thus remain free of TÜV monitoring and approval requirements. The relief valve must be designed according to the output of the connected steam boilers.
With a high condensate return flow, the pressure in the feed water container can often increase to more than 0.5 bar. Therefore, the JUMAG pressure degassing is equipped with an overflow valve that will open at a pressure between 0.2 bar and 0.5 bar to prevent frequent opening of the relief valve.
If the feed water container is overfilled, a level gauge on the level sensor sends a signal to a drain valve, which is opened accordingly.
If a vacuum occurs in the vessel, a magnetic valve and a mechanical non-return valve open. The magnetic valve installed under the feed water container takes over the functions for ventilation, overpressure limitation, overflow and under-pressure limitation.
Basicequipment
- Relief valve limited to pressure of 0.5 bar
- Integrated overflow valve that opens before the relief valve at approx. 0.3 bar
- Vacuum relief valve
- Angle seat valve for pressure maintenance
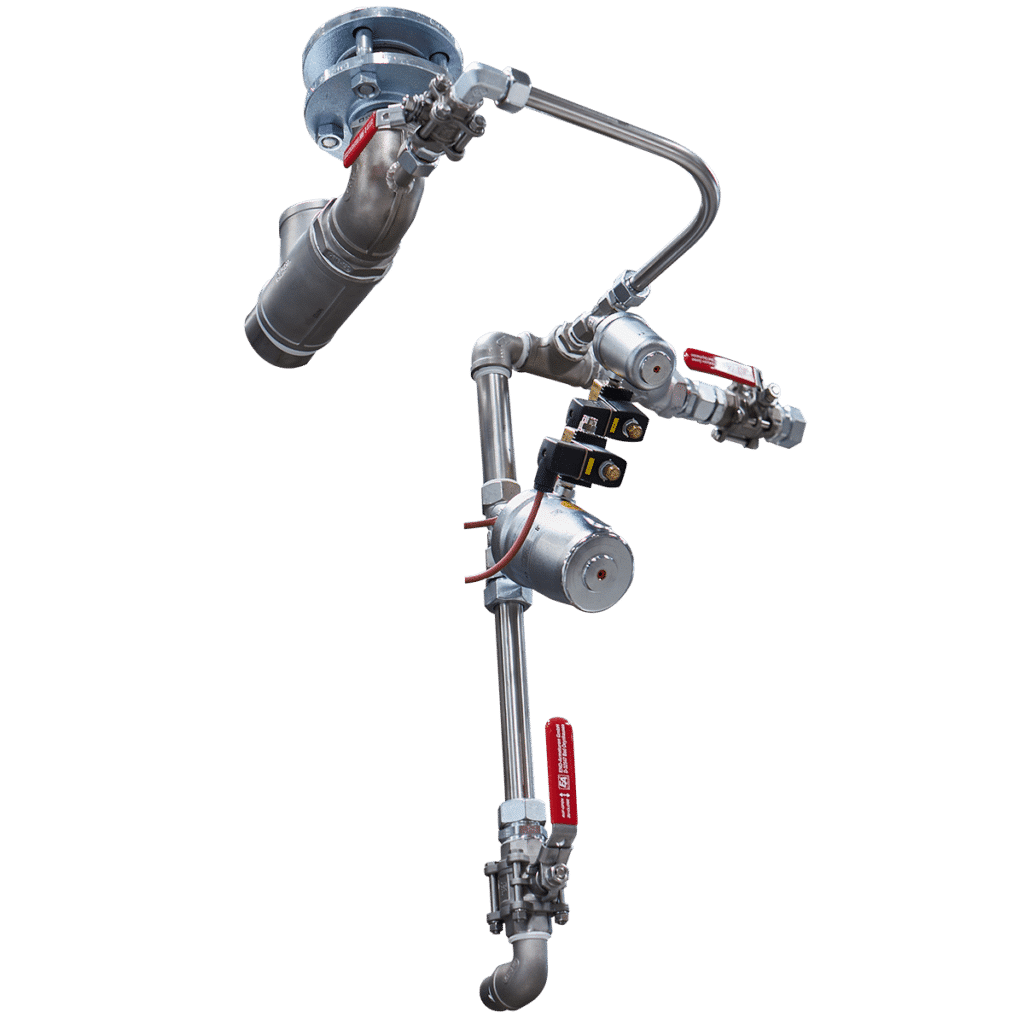